UF/IFAS Biofuel Pilot Plant
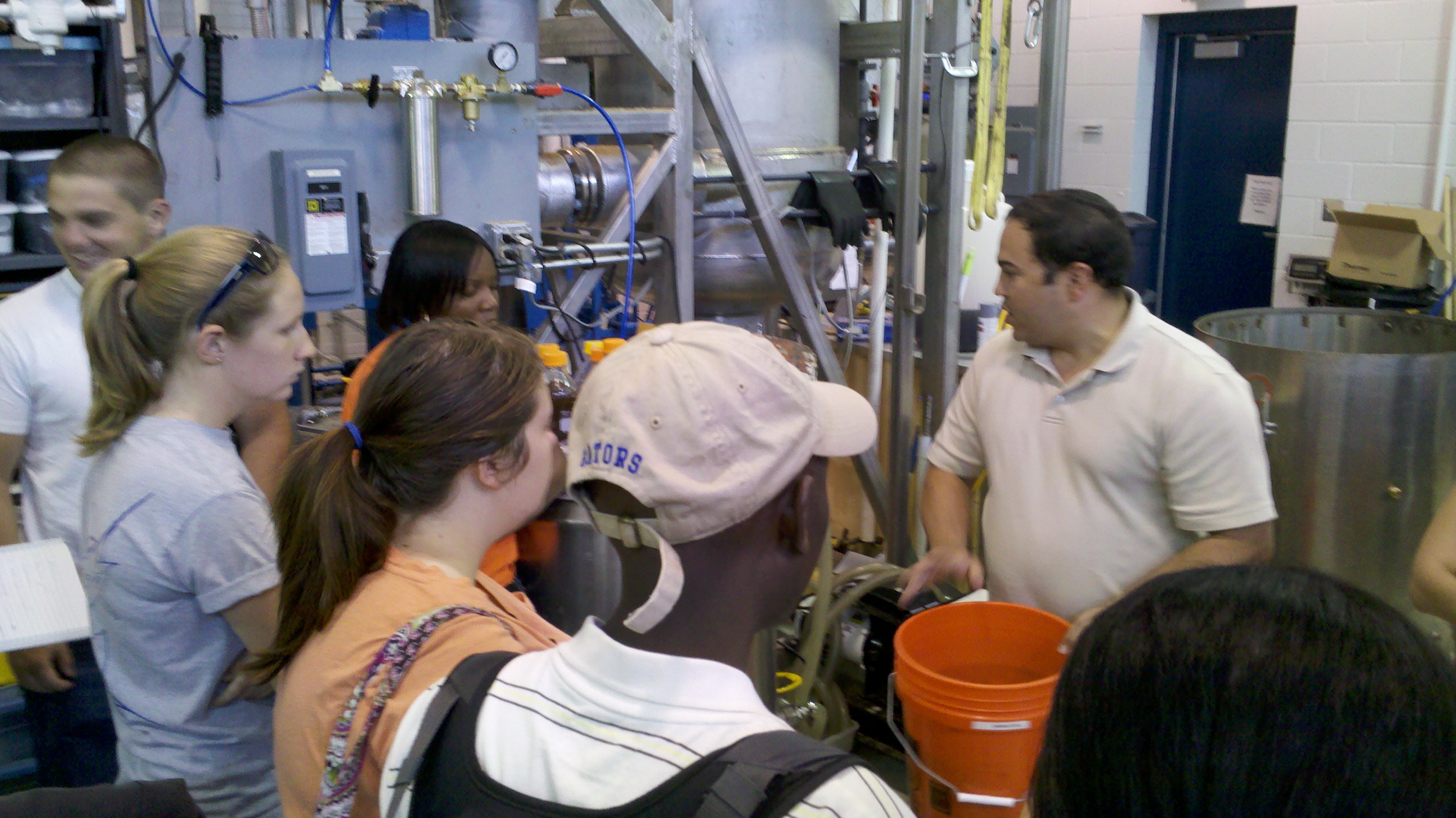
The BEST lab students visited the Bioethanol Plant; we were given a tour of the facility and shown how the various parts of the plant work. The idea of the plant is to convert biomass to energy. The biomass first goes through a pretreatment process, simultaneously an enzyme needs to be produced and injected into the pretreated plant biomass creating enzymatic hydrolysis. Next, the ethanol is fermented and distilled in order to produce ethanol fuel.
The main focus of this plant is to reduce the overall cost of the operation in order to make it a viable method of producing fuel on the commercial scale. The individuals who work at this plant are working on ways to reduce the cost of the pretreatment process as well as introducing biocatalysts which speed up the process and produce valuable chemicals as byproducts. Some of the benefits of these plants are improving the environment and energy independence for states that produce bioethanol.
There are several byproducts as a result of this process. One of these is succinic acid which is produced by E. coli. More byproducts are produced after fermentation; these can be converted into composites and fertilizers that can be returned to the sugarcane fields in order to make the process more sustainable.
The biomass that is utilized in this process is the pile of plants that are leftover after the sugar has been pressed out of the plants. Some of the problems the plant face is the variability in biomass. The biomass differs depending on what region it originates from, its moisture content, and the age of the biomass. The fresher biomass requires more inhibitors, yet if the biomass is too old, it is not viable. On average the dry biomass contains 50% cellulose, 25% lignin, and 25% hemicellulose.
The current pretreatment is done with an acid steam wash of the biomass. The plant has a 10 L reactor which reaches a temperature of 190 degrees C for 5 minutes in the process. After the pretreatment process a cellulose and lignin slurry is created. E. coli is the bacterium that is currently being used at this plant, specifically a strain that has been researched and selected for over many years. The plant is currently using 70 g of E. coli per 1 L of ethanol that is produced. Using their current methods the plant is able to produce 95% ethanol from glucose or xylose. They face a constant battle of balancing sugars and inhibitors. The organism that they are using has a high mutation rate and it can revert, although it will probably be outgrown by the original organism.
Overall I believe that the field trip was a great experience as we were able to see firsthand how biomass can be converted to ethanol. It was interesting to see what the material looked like at the different stages of the process. In the future the larger plant will be complete and the experiment will scale up once again to continue to perfect the process in order to bring the cost down to make it a viable fuel source.